
Lilypad gains registered trademark.
We’re pleased to announce that the Lilypad name and logo are now registered trademarks, following approval by the UK Intellectual Property Office! Learn more about Lilypad and how its shaping the future for offshore wind.
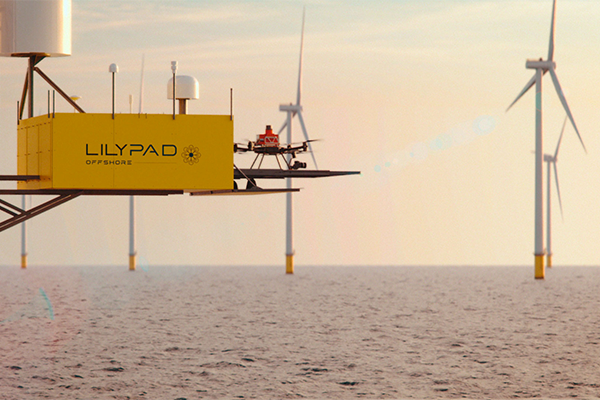